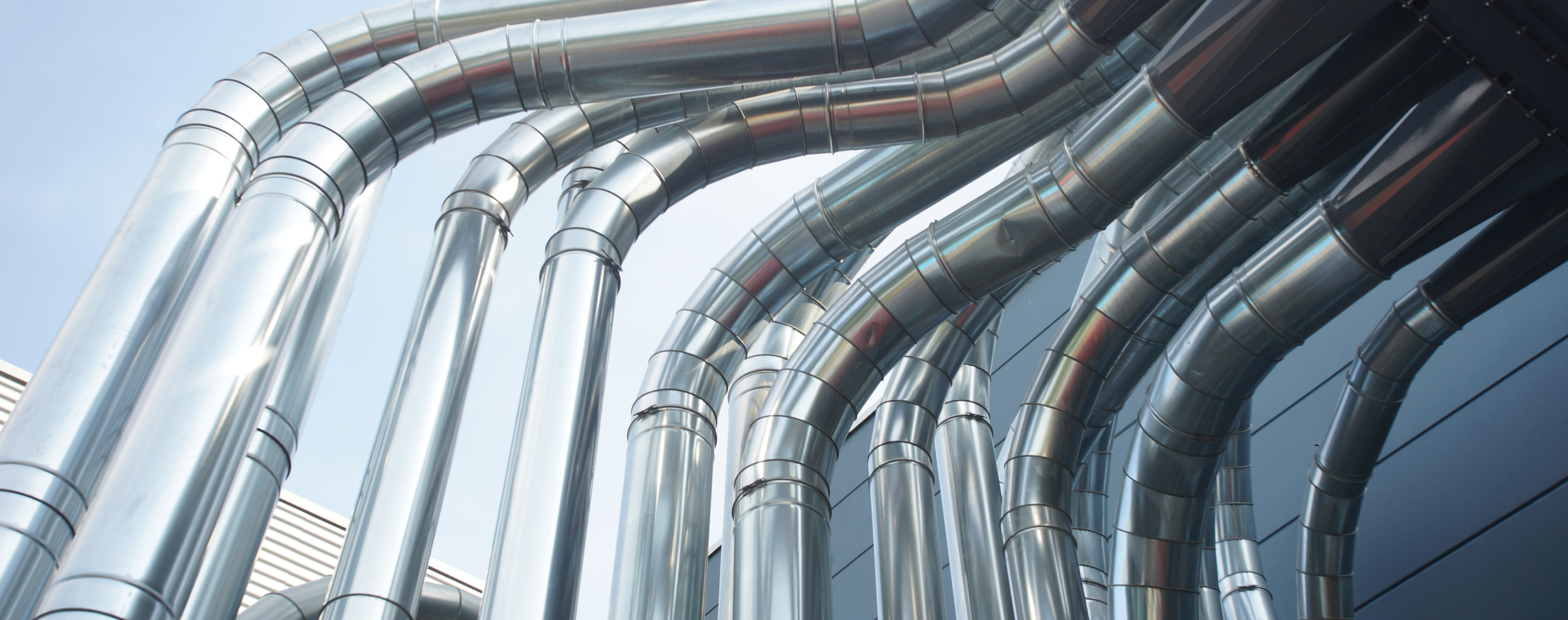
INDUSTRIAL
PLANTS – INDUSTRIAL DEDUSTING
Dust generated by production processes, regardless of their size, can be particularly harmful. In heavier particle sizes, dust tends to decant, downgrading work areas, while in lighter particle sizes it ‘floats’ in the environment, giving rise to a range of problems associated with the respiratory system.
An industrial dedusting system provides working environments with a higher level of comfort and better efficiency for production lines that are less subject to wear.
The main advantage is the achievement of cost savings, which are satisfactory and visible over time.
However, the implementation of an industrial dedusting plant requires a tailor-made design, which includes monitoring the concentration of dust and other materials in order to ensure efficiency, sustainable development and improved well-being for people.
Neuberg Srl has a wide range of solutions
that guarantees adequate, efficient and durable industrial dedusting.
The company handles dusts of various kinds such as food-grade, fibrous and non-fibrous, potentially explosive (ATEX directives).
Neuberg’s fully modular JKE, JKR and JKO dust collectors are designed for continuous high-speed filtration, meeting the requirements of current safety and environmental regulations. Requiring minimal cleaning and maintenance, they guarantee high efficiency.
Dust recovery process
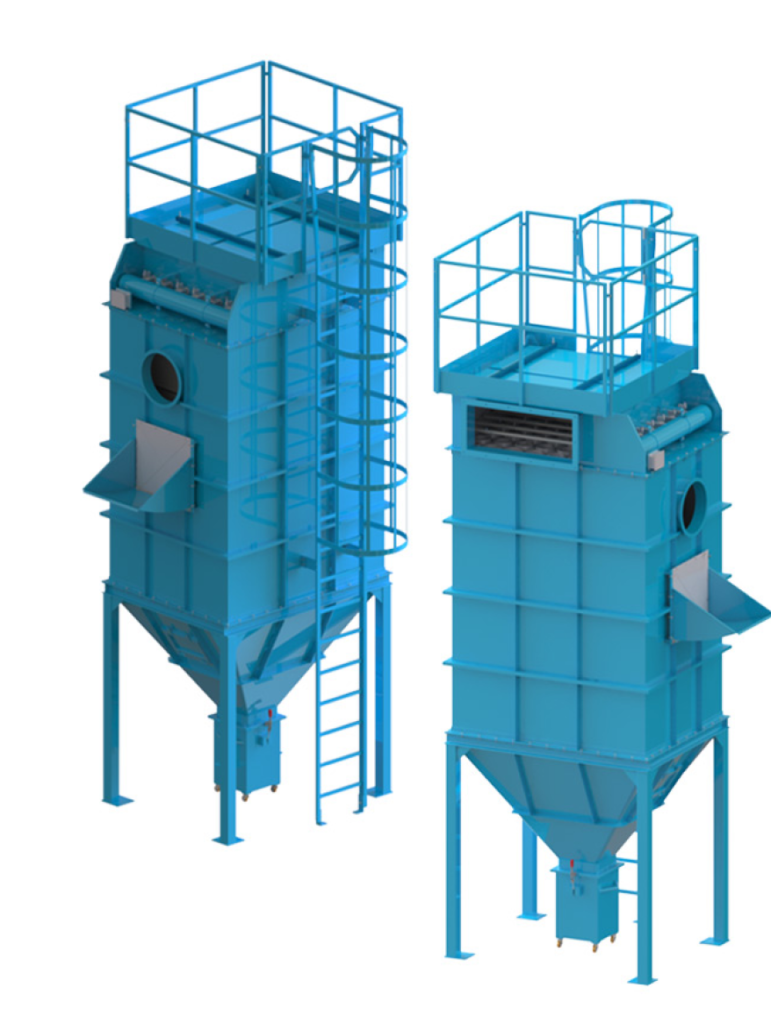
In the field of industrial dedusting, determining the level of ‘cleanliness’ one wishes to achieve often proves to be a thorny issue. Production lines, which are often huge and bulky and can therefore have different sources of dust formation, oblige the plant engineer to always make preventive plant assessments, which are necessary in order to be able to intercept the points of greatest dust exposure.
This is why the general effectiveness of a dedusting process depends on the design of the capture devices: the conformation of an extraction hood and the distance between it and the dust source are indispensable elements in determining the air volumes required for the correct sizing of the filtration system to be installed.
The different types of dust handled and their varying concentrations, the laws of fluid dynamics and experience in the field are indispensable elements for determining the optimal transport speed.
Conveying velocities that are too low can cause product settling, resulting in clogging, while velocities that are too high can generate risks of duct abrasion and high energy consumption.
The JKE range of dust collectors represents one of the core elements of Neuberg’s production.
The unique features of the elements that make up the filtration system (including the bag-holder basket) and the counter-current compressed air cleaning system, the different modularity of construction, which allows for maximum versatility, the high robustness of the structure built according to finite element FEM analysis, combined with venting and/or suppression devices, allow for the use of this equipment in the most diverse fields; even in environments where potentially explosive types of dust are handled (Atex Directives).
The dust filtered by the dust collectors proposed by Neuberg, which operate for almost all vacuum applications, is recovered by means of trolley-mounted, quick-release collection containers, or by means of dosing rotary valves of leading brands, with discharge into big bags, or even by means of automatic briquetting presses designed to press the dust itself into small, compact bricks.
This system, particularly compact and fully automatic, offers a much cleaner environment, easier dust management and a huge reduction in routine maintenance operations.
Fields of operation
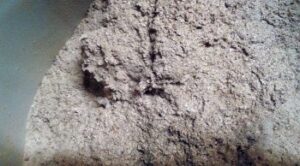
Various dusts
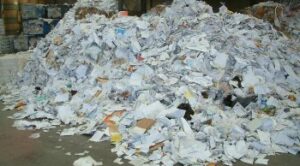
Recovery and
recycling
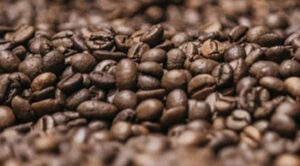