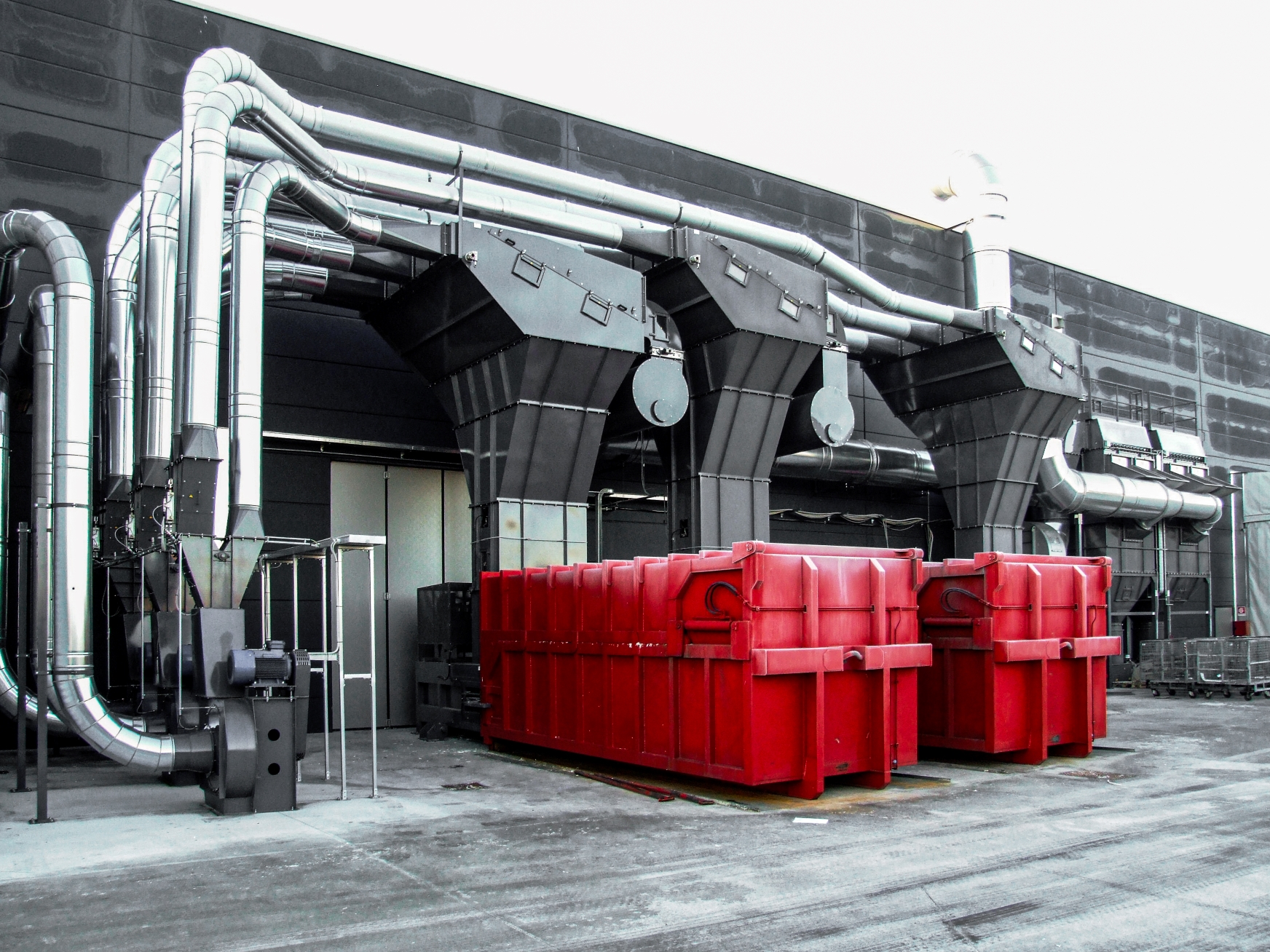
SUCTION OF
PLANTS – SUCTION OF OFFCUTS AND TRIMMINGS
The management of paper offcuts and trimmings represents a perfect model of circular economy. Approximately 60 per cent of national paper production, in fact, takes place using recycled fibres, thus prolonging natural resources, such as cellulose, and maintaining forests.
suction systems for offcuts and trimmings.
The company deals with the management and resolution of problems related to the collection, transport and storage of processing waste by means of complete cycle plants designed ad hoc: to create customised performance, designed for the specific needs of the customer to improve working conditions and realised in compliance with current regulations
Waste recovery process
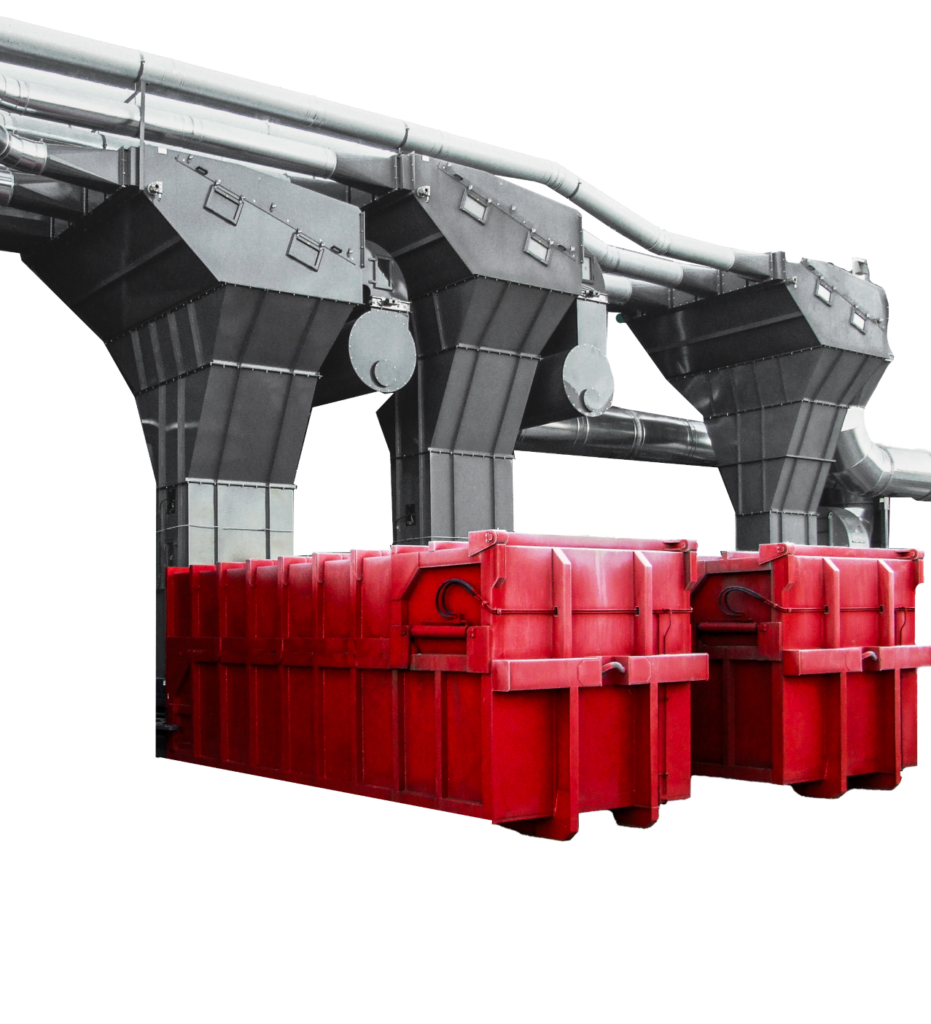
This phase requires the utmost care.
Depending on the different types of waste material to be vacuumed and the conformations of the individual machines, it is necessary to identify the most suitable system for correct capture. Mistaken size judgements, in fact, could result in a limitation of production performance as well as unavoidable and costly energy consumption.
Increasingly high performance is only guaranteed thanks to perfect system sizing and a highly aerodynamic construction profile, the result of experience gained over the years.
During the design phase, collecting as much data as possible on the type of products to be handled is crucial. In fact, one wrongly designed element generates problems that have a ‘domino effect’ throughout the entire suction and material transport circuit.
This is why the correct sizing of a system must be carefully analysed, from the intake to the storage of the material, right up to the expulsion of the air into the environment.
The result is the targeted choice of the type of fan to be used, the accessories to be provided as equipment (linear or serrated cutting blades, for example) and the related construction specifications.
In addition to improving performance in terms of efficiency, thanks to the rapid disassembly of the casing, the new design of the ‘CHOPPER EVO’ rip-off fans allows immediate variation of the type of orientation, up to SIX different types of configuration with the same product.
An industrial suction system is not limited to the use of tear-off fans inserted in its own process but, again by virtue of the different types of material to be treated and the speeds of the production lines, requires the use of ‘venturi’ conveying systems by means of injectors with a high aerodynamic profile, associated with centrifugal fans of primary international brands with efficiencies of over 85%.
In addition, some applications require the use of scissor cutting systems known as ‘cutters’, consisting of rotary blade cutters inserted into the plant’s suction circuit.
Here again, Neuberg opts for highly reliable international partners.
The choice of material conveying ducts (in terms of sizing, shapes and materials) allows constant uniformity of the transport speed of the product, limiting the pressure drops of the circuit itself to what is strictly necessary, an element which, combined with the targeted evaluation of the correct air flow rate, characterises a current absorption only for the specific requirements.
Various types of ‘air/material’ separation exist in the field of scrap extraction systems.
Studied on the basis of various experiences in this sector, PSM static separators have the prerogative of generating very low pressure drops (lower energy consumption required) compared to the use of common cyclones, and of not having any moving parts inside them (star valves) as is the case with rotary condensers on the market.
The static nature of such equipment means that there are no internal elements subject to wear and tear (e.g. sealing strips on the rotor blades and geared motors), thus avoiding jamming in contact with the material being conveyed (whose varying size or weight often constrains its proper functioning).
Obviously, this functionality is supported by the constant monitoring of the working conditions through pressure regulation systems with fully automatic management.
Before being expelled into the environment, the still partly dusty air extracted from the separators is conveyed into self-cleaning bag dust collectors.
In the process of treating the extracted pollutant, the following are of fundamental importance:
- the total knowledge of the pollutant: this allows the correct choice of filtering media to be determined each time;
- the structural resistance;
- the safety devices to be adopted for use in environments with potentially explosive dust, as per the risk assessment required by the current Atex directive (2014/34/EU).
The JKE range of dust collectors is unique in its design in that it allows for low compressed air consumption thanks to a unique model of sleeve basket and an effective counter-current cleaning system.
The complete customisation allows countless solutions to meet customer requirements.
Scrap and trimmings sucked in and conveyed to the ‘air/material’ separator are automatically discharged and collected in continuous horizontal presses, stationary presses with containers or compacting presses.
Neuberg has a strong sense of responsibility towards those who place an expectation in its solutions of a system that operates in a continuous cycle in total synergy with the production lines, an expectation confirmed by the large number of plants built and the many years of experience gained on them.
This responsibility has allowed the company to build up its know-how with extremely reliable partners producing such systems.
The winning strategy comes about when a company does not limit its investments solely to direct production machines, but when the farsightedness knows how to associate the correct suction system with production performance, which also becomes an integrated system of the entire production chain.
Sectors of intervention
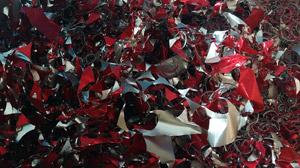
Aluminium offcuts
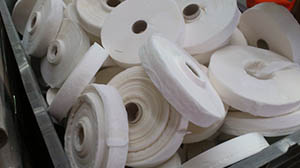
Toilet paper
(nonwovens)
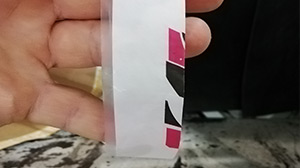